Understanding High Pressure Die Casting Suppliers
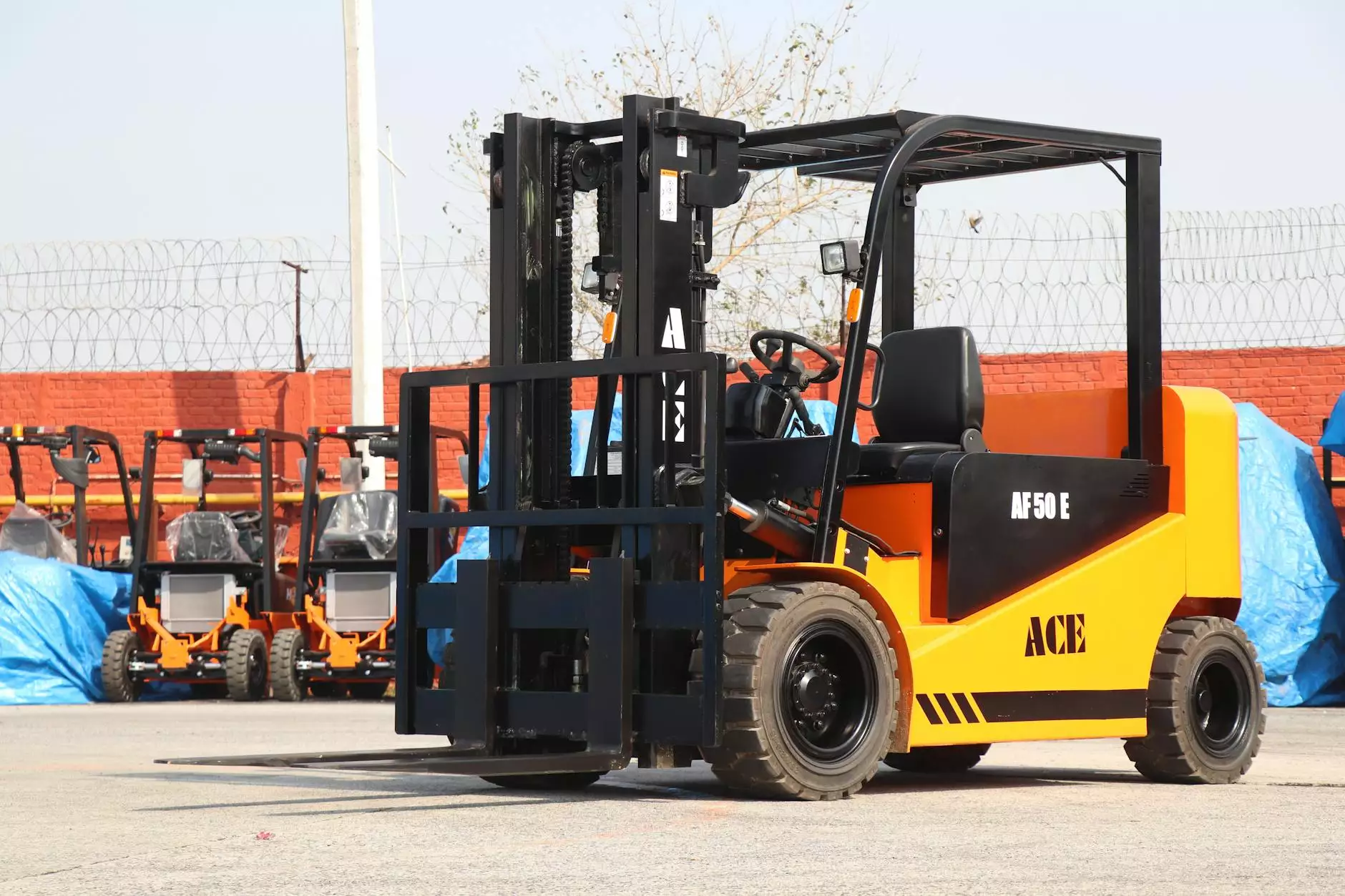
In today's competitive market, businesses need to leverage precision and quality when producing metal components. One of the most effective methods for creating high-quality parts is through high pressure die casting. This article delves into the world of high pressure die casting suppliers, explaining their role, benefits, and how to choose the right partners for your metal fabrication needs.
What is High Pressure Die Casting?
High pressure die casting is a manufacturing process where molten metal is injected into a mold at high pressure. This method is utilized primarily for producing aluminum and zinc parts, offering exceptional dimensional accuracy and surface finish. The process allows for the production of complex shapes and designs, making it ideal for various industries including automotive, aerospace, electronics, and consumer goods.
Advantages of High Pressure Die Casting
The advantages of utilizing high pressure die casting are numerous, including:
- High precision: Parts produced are highly accurate, with tight tolerances.
- Smooth surface finish: The process allows for a superior surface finish, reducing the need for post-production machining.
- Cost-effective: High-volume production reduces unit costs significantly.
- Complex geometries: Capable of producing intricate shapes that are difficult to achieve through other manufacturing processes.
- Rapid production rates: This method allows manufacturers to produce parts quickly, meeting consumer demands efficiently.
The Role of High Pressure Die Casting Suppliers
High pressure die casting suppliers play a crucial role in the manufacturing supply chain. They provide not only the materials and technologies needed for die casting but also expertise that can significantly enhance the production process. Here’s how they contribute:
- Material supply: Suppliers ensure that high-quality metals are available for the casting process, which is fundamental for producing durable parts.
- Equipment provision: They provide specialized machinery that ensures optimal conditions for die casting, which includes pressure levels, temperatures, and cooling times.
- Design and engineering support: Many suppliers offer engineering services to assist clients in designing molds that are optimized for production.
- Quality assurance: Suppliers typically perform rigorous testing and quality checks to ensure that the final products meet the necessary standards and specifications.
- Logistics and delivery: Efficient suppliers are equipped to handle the logistics involved in material supply and product delivery, ensuring timelines are met.
Choosing the Right High Pressure Die Casting Suppliers
Partnering with the right high pressure die casting supplier is crucial for the success of your project. Here are some key factors to consider:
1. Experience and Expertise
Look for suppliers with a proven track record in high pressure die casting. Experienced suppliers are more adept at managing complex projects and can provide valuable insights into best practices.
2. Quality Control Standards
Assess the supplier's quality control measures. Certification in industry standards, such as ISO 9001, indicates a commitment to maintaining high quality.
3. Technological Capabilities
Evaluate the technology and machinery that the supplier uses. Advanced equipment can make a significant difference in the quality and precision of the cast parts.
4. Customization Options
Your project may require custom solutions; therefore, it’s essential to choose suppliers that can offer tailored services and flexibility in production.
5. Logistics and Lead Times
Examine the supplier's logistics capabilities, including their ability to deliver products on time and handle unexpected delays. Reliable logistics ensure smoother operations.
6. Testimonials and Case Studies
Research testimonials from previous clients, and look for case studies that illustrate the supplier’s success in handling similar projects. Positive feedback can serve as a strong indicator of reliability.
Challenges Faced by High Pressure Die Casting Suppliers
While the high pressure die casting industry is lucrative, it’s not without challenges. Understanding these can help businesses navigate potential pitfalls:
- Material Variability: The quality of raw materials can fluctuate, impacting the final product's quality.
- Technological Advancements: Keeping up with the latest technologies requires significant investment, which can be prohibitive for smaller suppliers.
- Environmental Regulations: Adhering to increasing environmental regulations adds complexity and cost to operations.
- Market Competition: The rising number of suppliers in the market can drive prices down, affecting profit margins.
The Future of High Pressure Die Casting Suppliers
The future looks promising for high pressure die casting suppliers as industries increasingly seek efficient and cost-effective manufacturing solutions. Here are some trends expected to shape the industry:
1. Increased Automation
Automation in the die casting process will likely rise, improving production speeds and enhancing consistency and quality in the finished parts.
2. Adoption of Advanced Materials
With ongoing advancements in material science, suppliers will continue to explore the use of innovative materials that offer improved performance and sustainability.
3. Sustainability Practices
Environmental responsibility is becoming critical. Suppliers will adopt greener processes, such as recycling aluminum scrap and reducing energy consumption during production.
4. Digital Transformation
The industry is poised for a shift towards digital manufacturing solutions, utilizing data analytics, IoT, and AI to optimize production and predict maintenance needs.
Conclusion: Partnering for Success
For businesses looking to integrate high-quality metal components into their products, establishing partnerships with reliable high pressure die casting suppliers is essential. By understanding the advantages of this process, the pivotal role of suppliers, and how to select the right partners, businesses can enhance their manufacturing capabilities. Staying ahead in this ever-evolving landscape means continually assessing supplier relationships and embracing innovations in technology and sustainability. For more information on top-notch high pressure die casting services, explore deepmould.net, your trusted partner in metal fabrication.