Automotive Injection Molding Companies: Shaping the Future of Vehicles
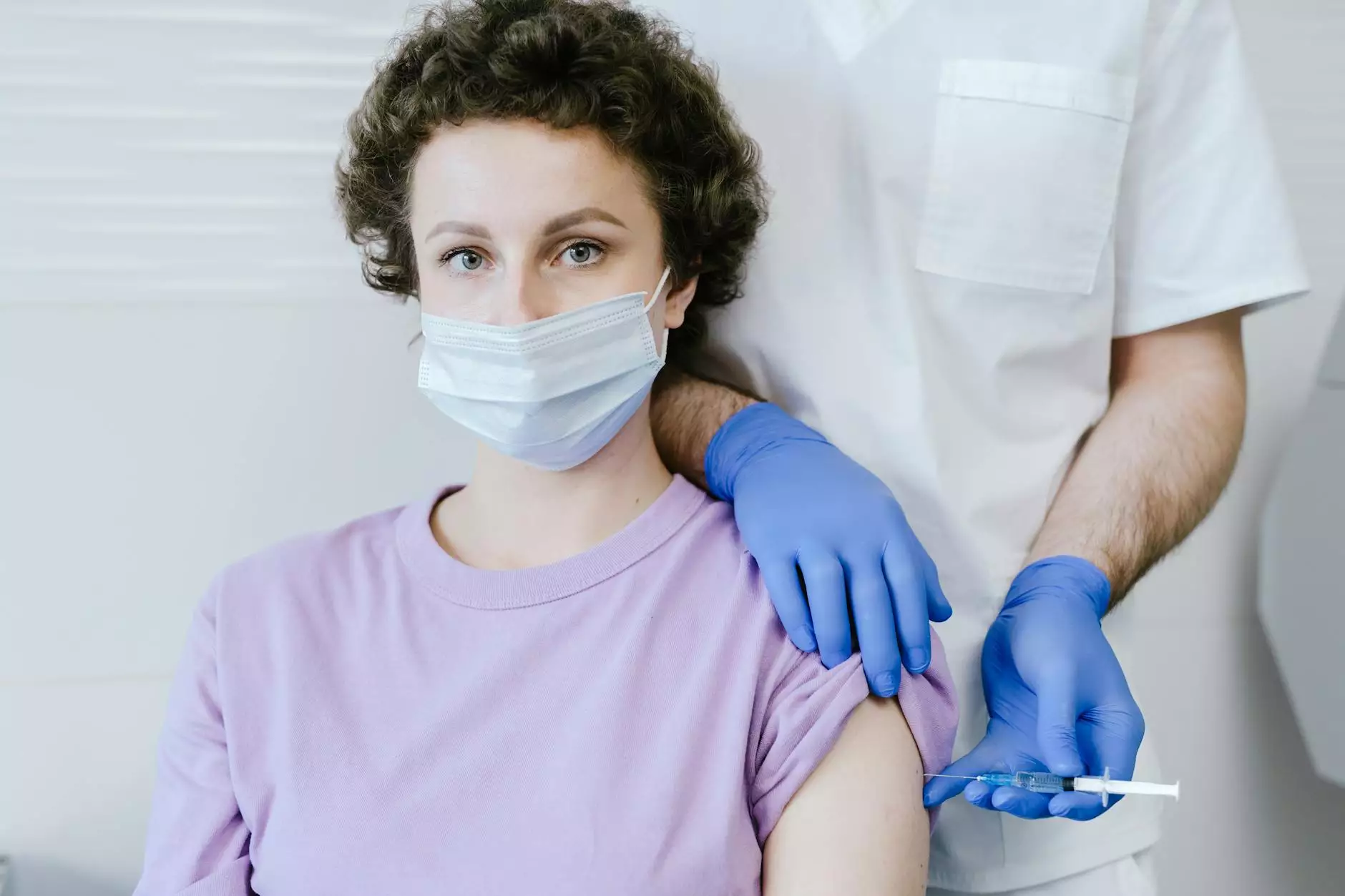
The automotive industry is one of the most dynamic sectors in the world, and at the forefront of this evolution are automotive injection molding companies. These specialized firms play a crucial role in manufacturing high-quality components that enhance both performance and aesthetics in vehicles. This article delves into the intricacies of injection molding processes, materials used, and the importance of these companies in the automotive supply chain.
Understanding Injection Molding
Injection molding is a manufacturing process used to produce parts by injecting molten material into a mold. This versatile technique is employed across various industries, but it is particularly vital in automotive production due to its efficiency, precision, and ability to create complex shapes.
How Injection Molding Works
The injection molding process consists of several key steps:
- Creating the Mold: Molds are designed based on the specifications of the parts needed. They are typically made from steel or aluminum, crafted to withstand high pressure and temperature.
- Heating the Material: Plastic materials, often thermoplastics, are heated until they melt into a liquid state, ready for injection.
- Injecting the Material: The molten plastic is injected into the mold cavity under high pressure, ensuring that it fills every corner of the mold.
- Cooling and Solidifying: The injection mold is cooled so that the plastic solidifies, taking on the desired shape.
- Removing the Part: Once cooled, the mold opens, and the finished part is ejected.
The Importance of Automotive Injection Molding Companies
Automotive injection molding companies are crucial to the automotive supply chain. They provide various benefits that significantly impact production efficiency and product quality:
1. Cost Effectiveness
Injection molding is highly cost-effective for manufacturing large quantities of parts. Once the mold is created, the cost per part decreases significantly, making it suitable for mass production.
2. Design Flexibility
This process allows for complex and intricate designs that would be challenging to achieve through other manufacturing methods. This design flexibility is ideal for meeting the sophisticated demands of modern vehicles.
3. Quality and Consistency
Injection molding ensures high precision and low tolerance levels, essential for critical automotive components. Consistency in manufacturing is crucial for safety and performance in vehicles.
4. Rapid Production
The speed of production in injection molding allows automotive manufacturers to respond quickly to market demands, reducing lead times significantly.
Key Materials Used in Automotive Injection Molding
Several materials are commonly used in the injection molding process, each with its unique properties that make them suitable for different automotive applications:
- Polypropylene (PP): Known for its lightweight and durability, making it ideal for interior parts.
- Polycarbonate (PC): Used for components requiring high impact resistance, such as headlamp covers.
- ABS Plastic: Offers a good balance of strength and flexibility, often used for trim parts.
- Nylon (PA): Valued for its strength and heat resistance, used in applications such as engine components.
Challenges Facing Automotive Injection Molding Companies
While the benefits of injection molding are significant, there are also challenges that companies must navigate to remain competitive:
1. Environmental Regulations
With increasing pressure to reduce environmental impact, automotive injection molding companies are exploring sustainable practices and materials that comply with stringent regulations.
2. Technological Advancements
Staying updated with the latest technological advancements is critical. Companies must invest in advanced machinery and software to maintain efficiency and improve production capabilities.
3. Skilled Labor Shortage
The industry faces a shortage of skilled workers proficient in modern injection molding techniques. Companies are investing in training programs to cultivate talent within the workforce.
Future Trends in Automotive Injection Molding
The future of automotive injection molding is shaped by several innovative trends:
1. Automation and Industry 4.0
Automation and the integration of Industry 4.0 technologies are poised to revolutionize the injection molding process. Smart factories that use IoT devices can monitor and optimize production in real-time.
2. Sustainable Materials
There is a growing trend towards using biodegradable and recycled materials in injection molding, aligning with global sustainability goals.
3. 3D Printing and Rapid Prototyping
3D printing is increasingly being utilized for creating molds and prototypes quickly, reducing time to market and enhancing design flexibility.
Why Choose DeepMould.net for Your Automotive Injection Molding Needs
DeepMould.net is a leading provider in the injection molding industry, specializing in automotive components. Here are several reasons to consider DeepMould for your next project:
- Expertise: A team of experienced professionals with in-depth knowledge of injection molding processes.
- State-of-the-Art Facilities: Equipped with the latest technology to ensure high-quality production.
- Quality Assurance: Rigorous testing and quality checks are performed to meet automotive standards.
- Customer-Focused: Dedicated to understanding client needs and providing tailored solutions.
Conclusion
In conclusion, automotive injection molding companies are integral to the production of modern vehicles. Through advancements in technology, innovative materials, and a focus on sustainability, these companies continue to push the boundaries of what's possible in automotive manufacturing. Organizations like DeepMould.net are leading the charge in delivering high-quality components that not only enhance vehicle performance but also align with the industry's evolving standards. As the automotive sector continues to grow and change, the role of injection molding will undoubtedly remain pivotal in shaping the future of vehicle production.